Common Issues Fixed by Packaging Machine Repair Services
Common Issues Fixed by Packaging Machine Repair Services
Blog Article
Quick and Reliable Packaging Equipment Repair Work Solutions to Minimize Downtime
In the competitive landscape of manufacturing, the efficiency of product packaging operations pivots on the integrity of machinery. Quick and reliable repair solutions are crucial in alleviating downtime, which can lead to considerable functional troubles and financial losses.
Significance of Timely Repairs
Timely repairs of product packaging devices are essential for maintaining functional efficiency and reducing downtime. In the fast-paced atmosphere of manufacturing and product packaging, also small breakdowns can lead to considerable delays and productivity losses. Addressing problems quickly makes sure that machines run at their optimal ability, consequently safeguarding the flow of procedures.
Moreover, prompt and normal upkeep can prevent the escalation of small troubles right into major failures, which usually incur higher repair service costs and longer downtimes. A positive strategy to equipment fixing not just preserves the integrity of the devices yet also enhances the total reliability of the production line.
Additionally, timely repair work contribute to the longevity of product packaging equipment. Makers that are serviced immediately are less most likely to endure from excessive deterioration, enabling organizations to maximize their financial investments. This is particularly vital in markets where high-speed product packaging is necessary, as the need for regular performance is critical.
Advantages of Reliable Solution Companies
Trustworthy service suppliers play a crucial duty in guaranteeing the smooth procedure of packaging devices. Their know-how not only improves the performance of repairs yet also contributes substantially to the long life of equipment. Dependable solution suppliers are outfitted with the technological expertise and experience essential to detect concerns accurately and carry out reliable options rapidly. This minimizes the danger of reoccuring issues and makes certain that equipments run at ideal efficiency levels.

Additionally, a trusted service copyright provides detailed support, including training and guidance for personnel on device procedure and upkeep finest practices. This not just equips workers however also grows a society of safety and performance within the organization. On the whole, the advantages of involving trustworthy service providers extend past instant repair work, positively affecting the entire functional workflow of packaging processes.
Usual Product Packaging Machine Issues
In the realm of packaging operations, different concerns can jeopardize the efficiency and performance of devices. One prevalent trouble is mechanical failing, usually coming from damage or inadequate upkeep. Components such as belts, equipments, and motors may fail, leading to break downs that stop production. One more common concern is misalignment, which can cause jams and unequal product packaging, impacting product quality and throughput.
Electric troubles can additionally disrupt packaging operations. Damaged wiring or malfunctioning sensors may cause irregular equipment habits, creating hold-ups and enhanced operational expenses. Furthermore, software application problems can prevent the equipment's programming, bring about operational inadequacies.
Inconsistent product circulation is one more important issue. This can arise from variants in product size, weight, or form, which might impact the machine's capacity to handle products precisely. Not enough training of drivers can aggravate these troubles, as inexperienced personnel may not acknowledge early indicators of malfunction or might misuse the devices.
Addressing these usual product packaging maker concerns without delay is necessary to preserving performance and guaranteeing a smooth procedure. Routine inspections and positive upkeep can dramatically minimize these worries, fostering a trustworthy packaging environment.
Tips for Reducing Downtime
To decrease downtime in product packaging procedures, carrying out a proactive maintenance technique is critical. Routinely arranged maintenance checks can identify possible concerns prior to they rise, guaranteeing equipments operate effectively. Developing a routine find out this here that consists of lubrication, calibration, and inspection of vital components can significantly minimize the frequency of unexpected break downs.
Educating staff to run machinery appropriately and identify early warning indicators of malfunction can also play a vital duty. Empowering drivers with the expertise to carry out standard troubleshooting can avoid small issues from creating significant hold-ups. Additionally, preserving a well-organized inventory of crucial extra components can speed up repairs, as awaiting parts can result in prolonged downtime.
In addition, documenting device efficiency and maintenance tasks can assist identify patterns and recurrent troubles, permitting targeted treatments. Including advanced monitoring technologies can offer real-time data, allowing predictive upkeep and minimizing the risk of abrupt failures.
Last but not least, cultivating open interaction in between operators and maintenance groups makes sure that any kind of irregularities are without delay reported and dealt with. By taking these proactive actions, services can improve operational performance and dramatically decrease downtime in product packaging procedures.
Picking the Right Repair Service Service
Picking the suitable repair service for product packaging machines is a vital choice that can considerably impact functional effectiveness. Begin by evaluating the provider's experience with your particular type of packaging devices.
Next, think about the service company's reputation. Looking for feedback from other businesses within your market can offer insights into dependability and quality. Certifications and collaborations with identified tools producers can additionally suggest a commitment to excellence.
Furthermore, examine their reaction time and accessibility. A provider who can use punctual support reduces downtime and keeps production circulation constant. It's also vital to ask about service warranty and service check assurances, which can mirror the confidence the copyright has in their job.
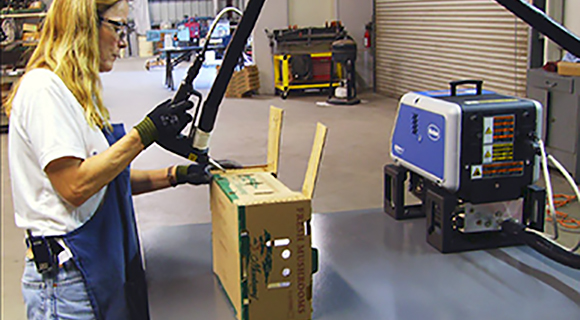
Final Thought
In verdict, the significance of trustworthy and fast packaging machine repair services can not be overemphasized, as they play a vital function in minimizing downtime and guaranteeing operational effectiveness. By prioritizing timely repairs and choosing dependable company, services can properly resolve usual problems and preserve efficiency. Applying positive maintenance practices and buying staff training more enhances the longevity of packaging equipment. Ultimately, a calculated approach to fix solutions promotes a more resistant manufacturing setting.
Timely repair services of product packaging makers are critical for keeping operational efficiency and minimizing downtime.Furthermore, prompt repairs add to the longevity of packaging equipment. In general, the benefits of involving trustworthy service carriers extend beyond instant repairs, positively affecting the whole operational process of packaging processes.
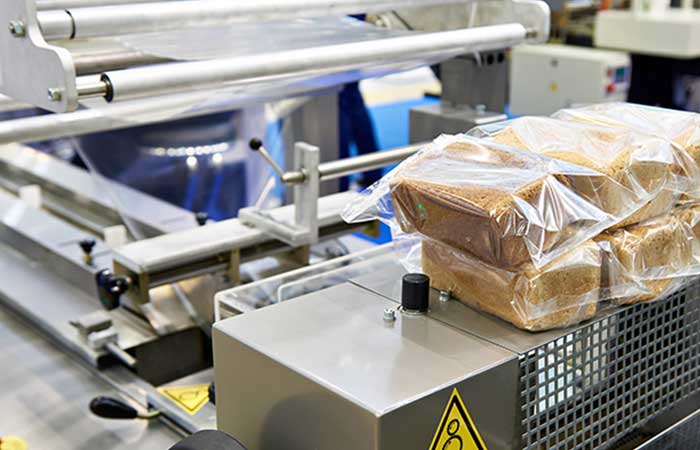
Report this page